Строительство субмарины из космического материала подстегнуло ОПК
Подлодке К-162 проекта 661 «Анчар» принадлежит рекорд подводной скорости – 44,7 узла (80,4 километра в час). Ее появление в середине 70-х годов XX века ознаменовало новый этап в строительстве советских подводных лодок – рождение отрасли морских титановых сплавов. В память о самоотверженных людях, которые строили атомоход, и в качестве примера уникальных достижений российской науки и техники еженедельник «ВПК» публикует воспоминания участника событий.
Первая в мире титановая субмарина – легендарная «Альфа» в марте 1989 года исключена из состава ВМФ, а в 2010-м утилизирована. На ней было решено много технических, конструкторских, научных и теоретических проблем, во многом благодаря ей созданы титановая промышленность, наука прочности и проектирования, наука технологии и материаловедения. Она обеспечила огромный вклад в общую культуру человечества потому, что ради ее создания трудились люди Москвы и Свердловска, Ленинграда и Киева, Новокузнецка и Ленинабада, Читы и Хабаровска – множество жителей нашего многонационального государства СССР, вложивших в нее душу и знания. Созданное после К-162 – подлодки проектов 705, 945, энергоустановки и многие другие системы, вобравшие наработки «Анчара», – живет и приносит пользу людям.
Абсолютный рекорд
Январь 1970 года. В Северодвинске мороз 22–26 градусов. Наша группа – члены государственной комиссии по приемке подводной лодки проекта 661 (заводской шифр – заказ 501) – ожидает выхода в море. В нее входят работники ЦКБ «Волна» (ЦКБ-16), ЦНИИ имени академика А. Н. Крылова и ЦНИИ КМ «Прометей», возглавляет группу Николай Иванович Антонов – главный конструктор по корпусу корабля.
Основная часть госкомиссии давно работает в море, закрываются различные акты или, как их называют, удостоверения, а мы ждем. Наша задача – участие в работе на завершающем этапе испытаний: погружение на предельную глубину и так называемая мерная миля, то есть фиксация скорости хода с разгона по длине, равной одной морской миле. Тесты должны проводиться в Кандалакшской губе, глубина которой в некоторых местах достигает 500 метров. Нам необходимо 400.
На ледоколе, минуя Соловецкий архипелаг, пошли на север. Здесь мы встретились с нашей лодкой, которая ходит уже с декабря. Подлодка остановилась, ледокол пришвартовался, и вся комиссия перешла в нее. Обстановка была, мягко выражаясь, напряженная. Штатная команда корабля – 60–67 человек, а на борту находились более 120 сдатчиков по разным системам и оборудованию. Когда ввалилась еще и наша команда, главный сдатчик от СМП Кузьма Михайлович Палкин схватился за голову, но Антонов распорядился просто: «Всем вниз, распаковывать измерительную аппаратуру, клеить датчики». С этой работой справились достаточно быстро. Заранее была подготовлена схема размещения датчиков по наиболее напряженным местам. Корпус корабля был весьма сложным – плоская носовая переборка с торпедными аппаратами, переход от цилиндрической части к восьмерочной, а затем к конической кормовой, много книц, подкреплений, каждое из которых являлось концентратором напряжений. Значительное количество этих мест мы оклеили датчиками и были уверены в достоверном определении напряженного состояния корпуса при глубоководных испытаниях.
Наконец поступила команда приступить к глубоководным испытаниям. Мы приготовились записывать показания датчиков. Обстановка торжественно напряженная. Николай Иванович был взволнован и каждые 10–15 метров погружения докладывал на центральный пост о максимальных замеренных напряжениях. Ко всеобщему удивлению, напряжения нарастали очень медленно. Все мы были участниками заводских испытаний опытных и штатных конструкций, когда нагружение производилось внутренним гидравлическим давлением. При таких тестах фиксировались напряжения выше не только предела текучести, но и предела прочности. Специалисты по расчетам прочности утверждали, что гидравлические испытания цилиндрических оболочек внутренним и внешним давлением абсолютно идентичны в «зеркальном отображении». Но в реальной конструкции в тех же «опасных» точках мы не фиксируем сколько-нибудь интенсивного роста напряжений. Я был на одном посту вместе с Владимиром Вульф-Гиршовичем Заком, ответственным за расчеты прочности корпуса подводной лодки. И они вдвоем с Антоновым докладывали на центральный пост: «Все в порядке, напряжения в норме». На рабочей глубине напряжения не превышали предельной нормы или были немного больше, и лодка пошла вверх.
Большим событием после глубоководных испытаний была так называемая мерная миля. Скоростное испытание показало, что на титановой лодке достигаются максимальные скоростные характеристики (более высокие, чем на стальных лодках). И когда при глубоководных испытаниях этой подводной лодки была получена рекордная скорость подводного хода (43 узла), все убедились, что СССР в очередной раз доказал миру свое техническое превосходство: глубже всех и быстрее всех. О нашей подводной лодке «Альфа» узнал весь мир, и сенат США начал всерьез обсуждать проблему подводного противостояния России.
Новая индустрия
В начале 50-х годов XX века военно-политические доктрины сверхдержав обосновывали построение двух основных систем: аэрокосмической для завоевания превосходства в воздухе и космосе, а также морской, обеспечивающей ракетный щит. Необходимым условием решения первой задачи был прорыв в области создания материалов с высокой удельной прочностью для всех типов летательных аппаратов. Ведущим направлением в этой области являлась технология производства изделий из титановых сплавов. Известно, что американский инженер Кроль запатентовал метод получения компактного титана в 1940 году.
Уже через несколько лет производство титана было освоено в СССР, причем на более высоком уровне. На Украине, Урале, в Казахстане были созданы производства по получению титановых концентратов и губчатого титана марок ТГ-1, ТГ-2. При этом советские специалисты, как правило, шли оригинальным путем. В Гиредмете (ныне ОАО «Гиредмет» ГНЦ РФ, ведущая научно-исследовательская и проектная организация материаловедческого профиля) и на Подольском химико-металлургическом заводе с привлечением ученых ЦНИИ КМ «Прометей» были разработаны различные технологии производства слитков. К середине 1955 года специалисты пришли к окончательному выводу: плавить титан нужно в дуговых печах, предложенных «Прометеем». Затем эту технологию передали на Верхне-Салдинский металлообрабатывающий завод (ВСМОЗ) в городе Верхняя Салда на Урале.
Для строительства подводной лодки длиной около 120 метров необходима была радикальная перестройка титановой индустрии. Инициатором в этом направлении выступило руководство ЦНИИ КМ «Прометей» – директор Георгий Ильич Капырин и главный инженер Игорь Васильевич Горынин, их решительно поддержал министр судостроительной промышленности Борис Евстафьевич Бутома. Эти люди проявили огромную дальновидность и гражданское мужество, принимая такое эпохальное решение. В качестве объекта для применения титана выбрали проект 661 разработки СПМБМ «Малахит» (в те времена ЦКБ-16). Одной из целей была отработка применения ПКР П-70 «Аметист» – первой в мире противокорабельной крылатой ракеты с «мокрым» стартом. Авторы проекта подлодки – Н. Н. Исанин, Н. Ф. Шульженко, В. Г. Тихомиров встретили предложение о его переработке в титановом исполнении без всякого энтузиазма. Титан для них был полной неизвестностью: меньший, чем у стали, модуль упругости, «холодная» ползучесть, иные методы сварки, полное отсутствие опыта применения в морских условиях. В таком же положении находились специалисты ЦНИИ имени академика А. Н. Крылова, ЦНИИ технологии судостроения, работники судостроительных верфей.
Тем не менее в 1958 году началась кардинальная перестройка титановой индустрии в стране. В ЦНИИ КМ «Прометей» появилось соответствующее подразделение – вначале отдел № 8, а затем отделы №№ 18, 19. Команда видных ученых создала научное направление – морские титановые сплавы. Коллективы титаномагниевых комбинатов Запорожского (ЗТМК) и Березниковского (БТМК) совместно со специалистами Всесоюзного алюминиево-магниевого института (ВАМИ), Гиредмета и при активном участии ученых ЦНИИ КМ «Прометей» провели большую работу по совершенствованию технологии производства титановой губки. Отечественная промышленность смогла производить крупные слитки массой четыре – шесть тонн для подлодок. Это была крупная победа. Следующей решалась проблема получения бездефектных слитков высокого качества.
Импорт, но с умом
Источников дефектов много – неправильный режим плавки, твердосплавные включения (карбиды вольфрама, окисленная губка, высокое содержание отходов в электродах и т. д.), усадочная рыхлость и возникновение раковин. Все эти сложности больших масс перешли к металлургам от «авиаторов». После реорганизации индустрии увеличивались объемы производства, размеры и развесы слитков. Их масса достигала четырех тонн и более.
Борьба за повышение качества губчатого титана и слитков обернулась для нас другой стороной. Снижение содержания примесей и включений привело к повышению пластичности, вязкости, уменьшению трещин в сварных соединениях – это был большой успех. Но одновременно снизилась прочность сплава. При строительстве подводной лодки проекта 661 предел текучести сплава марки 48-ОТЗ после «очистки» от вредных примесей уменьшился на десять процентов. В одной из партий листов были пропущены поверхностные дефекты («птички»), обнаруженные специалистами Севмаша (СМП), где строилась лодка. Позже начальник отдела Главного технического управления Госкомитета по судостроению А. С. Владимиров оперативно согласовал все вопросы по безвозмездному и срочному восполнению забракованной партии с Министерством авиационной промышленности, в ведении которого был ВСМОЗ.
Необходимо было решить, как восстановить предел текучести, не потеряв при этом достигнутых пластичности, вязкости и свариваемости. В кратчайшие сроки провели исследования влияния различных легирующих элементов на механические свойства сплавов системы Тi–Аl (и был выбран ванадий), разработаны технология изготовления алюминиево-ванадиевой лигатуры и введения ее в слиток, технология ковки слитка и прокатки листов, термообработки. Сплав получил наименование 48-ОТЗВ (с ванадием).
Для этого сплава были гарантированы необходимый предел текучести, достаточно высокие пластичность, вязкость, хорошая технологическая пластичность, свариваемость. Однако уже в самом начале выяснилось, что в нашей стране нет ванадия в тех количествах, которые необходимы для серийного производства сплава. Пятиокись ванадия марки ЧДА (чистый для анализа) импортировалась из Финляндии, и необходимо было решение Госплана СССР о закупке ее в больших количествах. Предлагалось альтернативное решение: эффективнее и дешевле (без импорта) вводить в сплав элементы, которые считались вредными: кислород, железо, кремний, но делать это строго регламентированными методами.
Снова неоценимую помощь оказал Владимиров. На совещании в Госплане он доходчиво объяснил, что ЦНИИ КМ «Прометей» не только решает задачу повышения прочности сплава, но учитывает свариваемость, технологичность, агрессивность среды и многие другие факторы. Поэтому его решение по легированию ванадием правильное. Впоследствии идея создания группы сплавов Ti–Al–V постоянно поддерживалась учеными авиационной промышленности. В конце концов сплав марки 48-ОТЗВ обрел права гражданства. С этого момента проблема ванадиевых лигатур стала главной для наших металлургов. Прошло немного времени, и было организовано их производство в Узбекистане и Таджикистане (Ленинабад, Чорух-Дайрон). Таким образом, наша страна перестала зависеть от поставок из-за границы.
Листы, трубы, дельные вещи
Получение слитка, химический состав, примеси, лигатуры – эти проблемы бесконечны, но подводная лодка, как и любое крупное инженерное сооружение, строится не из слитков, а из листов, поковок, профилей, труб, отливок. Возможности Верхне-Салдинского предприятия по листам исчерпались очень быстро, и необходимо было организовывать новые производства. Ленинградский совнархоз в 1959 году принимает постановление о развитии производственной базы по титану на Ижорском заводе и заводе «Большевик».
В чем была сложность? В Ленинградском совнархозе был один большой прокатный стан «Дуо-4000» с двумя валками длиной четыре метра. Приводился в движение паровой машиной, пущенной в 1903 году. На нем катали листы для постройки легендарной «Авроры» и других крейсеров этой серии. Этот стан был снабжен огромными мазутными печами, тихоходными рольгангами и кранами. В то время как зарубежные ученые писали (а мы у них учились), что титан нужно производить в «белых перчатках», нагревать в вакуумных печах или печах с контролируемой средой (аргон), мы решились на организацию производства титана в «стальных» условиях. Это позволило организовать серийное производство крупногабаритных листов массой до четырех и поковок массой до шести тонн, полностью обеспечив потребность в металле для строительства подводной лодки.
Другой задачей была организация производства тонких листов. В авиации лист толщиной пять-шесть миллиметров – это толстый, более 20 – уже плита. В судостроении толщина пять – десять миллиметров – тонкий лист, 40–100 – нормальный. Итак, нужно было организовать производство тонких листов шириной 1500–1700 миллиметров, длиной пять-шесть метров. Вместе с работниками нашего филиала в Жданове (ныне Мариуполь) специалисты ЦНИИ КМ «Прометей» радикально изменили технологию изготовления листов и полностью устранили такое явление, как водородное растрескивание. Комплекс «антиводородных» мероприятий был внедрен на всех заводах, производящих или перерабатывающих титан. В результате самоотверженной работы была достигнута надежная гарантия отсутствия трещин в сварных соединениях.
В подводной лодке, как на любом корабле, имеется большое количество труб. Это осушительные системы гидравлики, пожаротушения, забортной и пресной воды. Традиционно такие системы изготавливались из меди, медно-никелевых сплавов, углеродистой или нержавеющей стали. В титановом корпусе применять эти материалы нецелесообразно, так как в контакте с титаном при наличии морской воды эти металлы подвергаются усиленной гальванической коррозии.
Вначале была предпринята попытка производить трубы в Верхней Салде методом прессования. Однако в прессованных титановых трубах из-за низких антифрикционных свойств возникало большое количество дефектов. Поэтому в дальнейшем перешли на прокатные методы, а в Верхней Салде производили обточенную трубную заготовку. На Челябинском трубопрокатном заводе (ЧТПЗ) было организовано производство горячекатаных труб диаметром до 470 миллиметров, которые использовались как в трубных системах, работающих на полное забортное давление, так и в системах воздуха низкого, среднего и высокого давления (до 400 атмосфер). Из этих труб на волгоградском заводе «Баррикады» изготавливали баллоны ВВД (воздуха высокого давления). Имел место полуанекдотический случай.
Обычно для прокатки трубы берется трубная заготовка, в ней делается осевая полость на прошивном стане и затем катается труба. С. М. Шулькин предложил иную технологию: на ВСМОЗ высверливать в слитке осевую полость, стружку возвращать в плавку, а слиток с полостью, минуя прошивной стан, сразу запускать в прокатку трубы. Получалась значительная экономия средств и времени.
Это предложение было опробовано, установлена его эффективность, и все дружно приняли решение снизить цены на титановые баллоны (конечно, в расчете на хорошую премию). Вопрос всем казался настолько очевидным, что меня, тогда еще очень молодого и неопытного, снабдили всеми материалами и послали в бюро цен Госплана получить справку о снижении цен на баллоны. Я приехал, доложил этот вопрос какому-то начальнику и получил ответ, меня ошеломивший: «Баррикадам» на оставшиеся два года пятилетки было запланировано 438 баллонов и если цену баллонов уменьшить на 20–25 процентов, то завод по этой позиции не выполнит план «по валу» на эти самые проценты. Поэтому менять цены на исходе пятилетки нельзя, а план – это закон. И мы ждали конца пятилетки, откорректировали цены и план на следующие годы и только после этого получили долгожданную премию. Вот такие казусы были в прошлой жесткой плановой системе.
А далее пошли другие задачи. Кингстоны и другие клапаны, крышки торпедных аппаратов, приводы торпедных аппаратов, тарельчатые и витые пружины, амортизаторы и множество других изделий, которые на флоте именуются дельными вещами. Работники института прошли через все это. У них не было понятия: «Это не мое, не моя специальность». Они влезали во все и брались за решение любого вопроса, необходимого для постройки корабля. И в этом я вижу высокий интеллект коллектива ЦНИИ КМ «Прометей».
На Севмаше
Пока специалисты ЦНИИ КМ «Прометей» решали свои задачи на рудном, металлургическом, сварочном и других производствах, корабль строился и рос день ото дня. Главный конструктор по корпусу Н. И. Антонов ввел за правило минимум раз в два-три месяца бывать в цехе и участвовать в работе бригады, курирующей ход строительства.
Обычно это было и серьезно, и смешно. В те времена надевать каску при входе в зону работ было необязательно, и Антонов ею не пользовался. А лысина у него была, как солнечный диск. В это время возникла проблема «тычков». На корпус лодки изнутри приваривалось множество скобок для размещения на них кабелей и труб. Их было тысячи. Швы считались малоответственными, но наши сварщики относились к ним серьезно, так как если в этом шве будет окисление, то в прочном корпусе возникнет трещина и это может плохо кончиться. Как потом выяснилось, он хорошо понимал это и старался осмотреть шов приварки каждого «тычка». И вот, переходя из отсека в отсек, он выпрямлялся, ударяясь головой о «тычок», приваренный к перегородке или пайоле на борту, так что на лысине появлялась очередная ранка. Вначале это вызывало смех и у него, и у нас, его сопровождавших. Но когда мы проходили два-три отсека и на голове его появлялись кровоточащие раны, это было уже не смешно, но тем не менее он готов был целыми днями лазать по отсекам, забираясь в самые потаенные уголки, перепроверяя работу контролеров и сварщиков. У него было высокое чувство ответственности как главного конструктора корпуса первой в мире цельнотитановой подводной лодки.
А на заводе все прекрасно понимали, что при постройке такого сложного инженерного сооружения, как корпус подлодки из совершенно нового материала – титана, требовался новый подход. Надо отдать должное – директор СМП Е. П. Егоров, его заместители, конструкторы, строители, цеховые работники приложили много усилий для создания небывалого производства.
Цех № 42 стал поистине полигоном новизны: ежедневное мытье полов, отсутствие сквозняков, освещенность, чистая одежда сварщиков и других рабочих, высокая культура производства стали его отличительным признаком. Большой вклад в становление цеха внес Р. И. Утюшев – замначальника цеха по сварке. Много умения и души вложили в это дело замечательные специалисты – северяне Ю. Д. Каинов, М. И. Горелик, П. М. Гром, военпред Ю. А. Беликов, А. Е. Лейпурт и многие другие – технологи, мастера, рабочие.
В результате было создано самое совершенное сварочное производство с аргоногелиевой защитой. Аргонодуговая, ручная, полуавтоматическая, автоматическая и другие способы сварки стали обычными для всех работников цеха. Здесь были отработаны сварка погруженной дугой, сварка в «щель» (без разделки), требования к качеству аргона (точка росы), появилась новая профессия – сварщик по защите обратной стороны шва (поддувальщик).
В этом цехе возникла такая эффективная форма сотрудничества производственных и научно-исследовательских коллективов, как постоянно действующая бригада. Возглавлял ее П. М. Гром, от ЦНИИ-48 постоянными членами были Б. В. Кудояров, И. С. Фатиев, З. Ф. Загудаева, от СМП Р. И. Утюшев, от ЦНИИ-136 Б. А. Эрам и другие классные специалисты. Все вопросы, возникавшие при постройке корпуса и его насыщении, эта бригада решала на месте. А вопросов было множество: например, как маркировать детали – клеймами или керном, можно ли их сваривать без сквозного проплавления (то есть допускать конструктивный концентратор), как приваривать «бобышки» (вертикальные стерженьки), как ремонтировать швы с вольфрамовыми включениями и окисленными участками, как защищать обратную сторону шва при сварке стабилизаторов.
Были тысячи вопросов, которые в основном решались на основе инженерной интуиции и производственного опыта. Это был принципиально новый подход к постройке таких сложных инженерных сооружений, как корпуса подлодок из нового материала, с использованием новых способов сварки. И он себя оправдал, так как позволил оперативно и четко принимать технические решения, не задерживая производство. И вот пришло время проводить гидравлические испытания. Первым тестировали средний блок. Вечером цех № 42 был освобожден от всех работников, остались только члены государственной комиссии и бригада специалистов, обеспечивавшая нагружение. Вот ступенями повышается давление: 10–20–30–40 атмосфер, выдержка... и вдруг за пять минут до конца выдержки происходит разрушение. У всех состояние шока.
На следующий день воду слили и обнаружили, что трещина длиной почти два метра возникла в обшивке – на границе между двумя комингсами килевых кингстонов, расположенных очень близко друг к другу и к плоской переборке. Этот узел был очень жестким и, естественно, стал местом концентрации напряжений, когда упругоподатливая обшивка стала расширяться при внутреннем нагружении. Здесь и произошло разрушение. Впоследствии подобные трещины возникали и в других «жесткостях» – в районе окончания поперечного шельфа как основы для турбины, в окончании книц.
На этом опыте возникла новая концепция проектирования оболочковых конструкций: исключаются «жесткие» окончания, появляются «мягкие» кницы, плавные переходы от жестких деталей к упругоподатливым и т. д. Эта идея в полной мере была реализована затем В. Г. Тихомировым и В. В. Крыловым при проектировании ПК подводной лодки проекта 705 «Лира» (по кодификации НАТО – «Альфа»). С учетом опыта Н. И. Антонова их корпус оказался идеальным. Но после всех неприятностей корпус подлодки проекта 661 был доведен до совершенства и все блоки прошли испытания.
Проект «Анчар» был необычен не только корпусом из титанового сплава. На лодке впервые были применены ПКР «Аметист» с подводным стартом и забортным расположением шахт, созданы гидроакустическая станция и гидроакустический комплекс, которые в сочетании с торпедными аппаратами предопределили совершенно новую форму носовой оконечности – шаровую вместо привычно остроносой. Это логично привело к каплевидной форме корпуса до кормы. Двойная энергоустановка с двумя турбозубчатыми агрегатами и двумя линиями гребных валов привела к новой форме кормовой оконечности (так называемые штаны), когда два длинных конуса заканчивались гребными винтами. Изящное ограждение рубки, кормовой стабилизатор придавали кораблю элегантно-красивый вид. В нем было хорошо и внутри: cияющие чистотой кают-компания, комната отдыха, душевая, сауна, титановые унитазы. Антонов очень гордился тем, что на подлодке созданы условия для экипажа не хуже, чем на надводном корабле. Это потом подтвердил командир лодки, который служил на ней с момента постройки, ходил и в Арктику, и в Антарктиду, и в Карибское море, и в Тихий океан.
Подлодке К-162 проекта 661 «Анчар» принадлежит рекорд подводной скорости – 44,7 узла (80,4 километра в час). Ее появление в середине 70-х годов XX века ознаменовало новый этап в строительстве советских подводных лодок – рождение отрасли морских титановых сплавов. В память о самоотверженных людях, которые строили атомоход, и в качестве примера уникальных достижений российской науки и техники еженедельник «ВПК» публикует воспоминания участника событий.
Первая в мире титановая субмарина – легендарная «Альфа» в марте 1989 года исключена из состава ВМФ, а в 2010-м утилизирована. На ней было решено много технических, конструкторских, научных и теоретических проблем, во многом благодаря ей созданы титановая промышленность, наука прочности и проектирования, наука технологии и материаловедения. Она обеспечила огромный вклад в общую культуру человечества потому, что ради ее создания трудились люди Москвы и Свердловска, Ленинграда и Киева, Новокузнецка и Ленинабада, Читы и Хабаровска – множество жителей нашего многонационального государства СССР, вложивших в нее душу и знания. Созданное после К-162 – подлодки проектов 705, 945, энергоустановки и многие другие системы, вобравшие наработки «Анчара», – живет и приносит пользу людям.
Абсолютный рекорд
Январь 1970 года. В Северодвинске мороз 22–26 градусов. Наша группа – члены государственной комиссии по приемке подводной лодки проекта 661 (заводской шифр – заказ 501) – ожидает выхода в море. В нее входят работники ЦКБ «Волна» (ЦКБ-16), ЦНИИ имени академика А. Н. Крылова и ЦНИИ КМ «Прометей», возглавляет группу Николай Иванович Антонов – главный конструктор по корпусу корабля.
Основная часть госкомиссии давно работает в море, закрываются различные акты или, как их называют, удостоверения, а мы ждем. Наша задача – участие в работе на завершающем этапе испытаний: погружение на предельную глубину и так называемая мерная миля, то есть фиксация скорости хода с разгона по длине, равной одной морской миле. Тесты должны проводиться в Кандалакшской губе, глубина которой в некоторых местах достигает 500 метров. Нам необходимо 400.
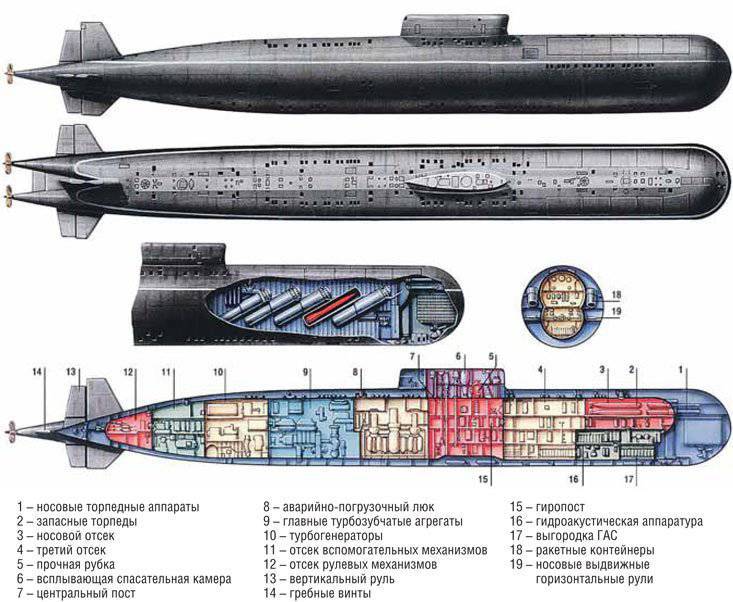
На ледоколе, минуя Соловецкий архипелаг, пошли на север. Здесь мы встретились с нашей лодкой, которая ходит уже с декабря. Подлодка остановилась, ледокол пришвартовался, и вся комиссия перешла в нее. Обстановка была, мягко выражаясь, напряженная. Штатная команда корабля – 60–67 человек, а на борту находились более 120 сдатчиков по разным системам и оборудованию. Когда ввалилась еще и наша команда, главный сдатчик от СМП Кузьма Михайлович Палкин схватился за голову, но Антонов распорядился просто: «Всем вниз, распаковывать измерительную аппаратуру, клеить датчики». С этой работой справились достаточно быстро. Заранее была подготовлена схема размещения датчиков по наиболее напряженным местам. Корпус корабля был весьма сложным – плоская носовая переборка с торпедными аппаратами, переход от цилиндрической части к восьмерочной, а затем к конической кормовой, много книц, подкреплений, каждое из которых являлось концентратором напряжений. Значительное количество этих мест мы оклеили датчиками и были уверены в достоверном определении напряженного состояния корпуса при глубоководных испытаниях.
Наконец поступила команда приступить к глубоководным испытаниям. Мы приготовились записывать показания датчиков. Обстановка торжественно напряженная. Николай Иванович был взволнован и каждые 10–15 метров погружения докладывал на центральный пост о максимальных замеренных напряжениях. Ко всеобщему удивлению, напряжения нарастали очень медленно. Все мы были участниками заводских испытаний опытных и штатных конструкций, когда нагружение производилось внутренним гидравлическим давлением. При таких тестах фиксировались напряжения выше не только предела текучести, но и предела прочности. Специалисты по расчетам прочности утверждали, что гидравлические испытания цилиндрических оболочек внутренним и внешним давлением абсолютно идентичны в «зеркальном отображении». Но в реальной конструкции в тех же «опасных» точках мы не фиксируем сколько-нибудь интенсивного роста напряжений. Я был на одном посту вместе с Владимиром Вульф-Гиршовичем Заком, ответственным за расчеты прочности корпуса подводной лодки. И они вдвоем с Антоновым докладывали на центральный пост: «Все в порядке, напряжения в норме». На рабочей глубине напряжения не превышали предельной нормы или были немного больше, и лодка пошла вверх.
Большим событием после глубоководных испытаний была так называемая мерная миля. Скоростное испытание показало, что на титановой лодке достигаются максимальные скоростные характеристики (более высокие, чем на стальных лодках). И когда при глубоководных испытаниях этой подводной лодки была получена рекордная скорость подводного хода (43 узла), все убедились, что СССР в очередной раз доказал миру свое техническое превосходство: глубже всех и быстрее всех. О нашей подводной лодке «Альфа» узнал весь мир, и сенат США начал всерьез обсуждать проблему подводного противостояния России.
Новая индустрия
В начале 50-х годов XX века военно-политические доктрины сверхдержав обосновывали построение двух основных систем: аэрокосмической для завоевания превосходства в воздухе и космосе, а также морской, обеспечивающей ракетный щит. Необходимым условием решения первой задачи был прорыв в области создания материалов с высокой удельной прочностью для всех типов летательных аппаратов. Ведущим направлением в этой области являлась технология производства изделий из титановых сплавов. Известно, что американский инженер Кроль запатентовал метод получения компактного титана в 1940 году.
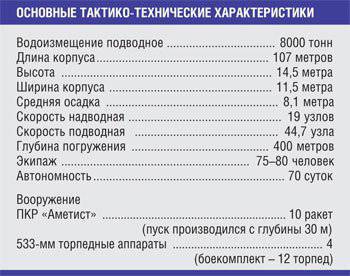
Для строительства подводной лодки длиной около 120 метров необходима была радикальная перестройка титановой индустрии. Инициатором в этом направлении выступило руководство ЦНИИ КМ «Прометей» – директор Георгий Ильич Капырин и главный инженер Игорь Васильевич Горынин, их решительно поддержал министр судостроительной промышленности Борис Евстафьевич Бутома. Эти люди проявили огромную дальновидность и гражданское мужество, принимая такое эпохальное решение. В качестве объекта для применения титана выбрали проект 661 разработки СПМБМ «Малахит» (в те времена ЦКБ-16). Одной из целей была отработка применения ПКР П-70 «Аметист» – первой в мире противокорабельной крылатой ракеты с «мокрым» стартом. Авторы проекта подлодки – Н. Н. Исанин, Н. Ф. Шульженко, В. Г. Тихомиров встретили предложение о его переработке в титановом исполнении без всякого энтузиазма. Титан для них был полной неизвестностью: меньший, чем у стали, модуль упругости, «холодная» ползучесть, иные методы сварки, полное отсутствие опыта применения в морских условиях. В таком же положении находились специалисты ЦНИИ имени академика А. Н. Крылова, ЦНИИ технологии судостроения, работники судостроительных верфей.
Тем не менее в 1958 году началась кардинальная перестройка титановой индустрии в стране. В ЦНИИ КМ «Прометей» появилось соответствующее подразделение – вначале отдел № 8, а затем отделы №№ 18, 19. Команда видных ученых создала научное направление – морские титановые сплавы. Коллективы титаномагниевых комбинатов Запорожского (ЗТМК) и Березниковского (БТМК) совместно со специалистами Всесоюзного алюминиево-магниевого института (ВАМИ), Гиредмета и при активном участии ученых ЦНИИ КМ «Прометей» провели большую работу по совершенствованию технологии производства титановой губки. Отечественная промышленность смогла производить крупные слитки массой четыре – шесть тонн для подлодок. Это была крупная победа. Следующей решалась проблема получения бездефектных слитков высокого качества.
Импорт, но с умом
Источников дефектов много – неправильный режим плавки, твердосплавные включения (карбиды вольфрама, окисленная губка, высокое содержание отходов в электродах и т. д.), усадочная рыхлость и возникновение раковин. Все эти сложности больших масс перешли к металлургам от «авиаторов». После реорганизации индустрии увеличивались объемы производства, размеры и развесы слитков. Их масса достигала четырех тонн и более.
Борьба за повышение качества губчатого титана и слитков обернулась для нас другой стороной. Снижение содержания примесей и включений привело к повышению пластичности, вязкости, уменьшению трещин в сварных соединениях – это был большой успех. Но одновременно снизилась прочность сплава. При строительстве подводной лодки проекта 661 предел текучести сплава марки 48-ОТЗ после «очистки» от вредных примесей уменьшился на десять процентов. В одной из партий листов были пропущены поверхностные дефекты («птички»), обнаруженные специалистами Севмаша (СМП), где строилась лодка. Позже начальник отдела Главного технического управления Госкомитета по судостроению А. С. Владимиров оперативно согласовал все вопросы по безвозмездному и срочному восполнению забракованной партии с Министерством авиационной промышленности, в ведении которого был ВСМОЗ.
Необходимо было решить, как восстановить предел текучести, не потеряв при этом достигнутых пластичности, вязкости и свариваемости. В кратчайшие сроки провели исследования влияния различных легирующих элементов на механические свойства сплавов системы Тi–Аl (и был выбран ванадий), разработаны технология изготовления алюминиево-ванадиевой лигатуры и введения ее в слиток, технология ковки слитка и прокатки листов, термообработки. Сплав получил наименование 48-ОТЗВ (с ванадием).
Для этого сплава были гарантированы необходимый предел текучести, достаточно высокие пластичность, вязкость, хорошая технологическая пластичность, свариваемость. Однако уже в самом начале выяснилось, что в нашей стране нет ванадия в тех количествах, которые необходимы для серийного производства сплава. Пятиокись ванадия марки ЧДА (чистый для анализа) импортировалась из Финляндии, и необходимо было решение Госплана СССР о закупке ее в больших количествах. Предлагалось альтернативное решение: эффективнее и дешевле (без импорта) вводить в сплав элементы, которые считались вредными: кислород, железо, кремний, но делать это строго регламентированными методами.
Снова неоценимую помощь оказал Владимиров. На совещании в Госплане он доходчиво объяснил, что ЦНИИ КМ «Прометей» не только решает задачу повышения прочности сплава, но учитывает свариваемость, технологичность, агрессивность среды и многие другие факторы. Поэтому его решение по легированию ванадием правильное. Впоследствии идея создания группы сплавов Ti–Al–V постоянно поддерживалась учеными авиационной промышленности. В конце концов сплав марки 48-ОТЗВ обрел права гражданства. С этого момента проблема ванадиевых лигатур стала главной для наших металлургов. Прошло немного времени, и было организовано их производство в Узбекистане и Таджикистане (Ленинабад, Чорух-Дайрон). Таким образом, наша страна перестала зависеть от поставок из-за границы.
Листы, трубы, дельные вещи
Получение слитка, химический состав, примеси, лигатуры – эти проблемы бесконечны, но подводная лодка, как и любое крупное инженерное сооружение, строится не из слитков, а из листов, поковок, профилей, труб, отливок. Возможности Верхне-Салдинского предприятия по листам исчерпались очень быстро, и необходимо было организовывать новые производства. Ленинградский совнархоз в 1959 году принимает постановление о развитии производственной базы по титану на Ижорском заводе и заводе «Большевик».
В чем была сложность? В Ленинградском совнархозе был один большой прокатный стан «Дуо-4000» с двумя валками длиной четыре метра. Приводился в движение паровой машиной, пущенной в 1903 году. На нем катали листы для постройки легендарной «Авроры» и других крейсеров этой серии. Этот стан был снабжен огромными мазутными печами, тихоходными рольгангами и кранами. В то время как зарубежные ученые писали (а мы у них учились), что титан нужно производить в «белых перчатках», нагревать в вакуумных печах или печах с контролируемой средой (аргон), мы решились на организацию производства титана в «стальных» условиях. Это позволило организовать серийное производство крупногабаритных листов массой до четырех и поковок массой до шести тонн, полностью обеспечив потребность в металле для строительства подводной лодки.
Другой задачей была организация производства тонких листов. В авиации лист толщиной пять-шесть миллиметров – это толстый, более 20 – уже плита. В судостроении толщина пять – десять миллиметров – тонкий лист, 40–100 – нормальный. Итак, нужно было организовать производство тонких листов шириной 1500–1700 миллиметров, длиной пять-шесть метров. Вместе с работниками нашего филиала в Жданове (ныне Мариуполь) специалисты ЦНИИ КМ «Прометей» радикально изменили технологию изготовления листов и полностью устранили такое явление, как водородное растрескивание. Комплекс «антиводородных» мероприятий был внедрен на всех заводах, производящих или перерабатывающих титан. В результате самоотверженной работы была достигнута надежная гарантия отсутствия трещин в сварных соединениях.
В подводной лодке, как на любом корабле, имеется большое количество труб. Это осушительные системы гидравлики, пожаротушения, забортной и пресной воды. Традиционно такие системы изготавливались из меди, медно-никелевых сплавов, углеродистой или нержавеющей стали. В титановом корпусе применять эти материалы нецелесообразно, так как в контакте с титаном при наличии морской воды эти металлы подвергаются усиленной гальванической коррозии.
Вначале была предпринята попытка производить трубы в Верхней Салде методом прессования. Однако в прессованных титановых трубах из-за низких антифрикционных свойств возникало большое количество дефектов. Поэтому в дальнейшем перешли на прокатные методы, а в Верхней Салде производили обточенную трубную заготовку. На Челябинском трубопрокатном заводе (ЧТПЗ) было организовано производство горячекатаных труб диаметром до 470 миллиметров, которые использовались как в трубных системах, работающих на полное забортное давление, так и в системах воздуха низкого, среднего и высокого давления (до 400 атмосфер). Из этих труб на волгоградском заводе «Баррикады» изготавливали баллоны ВВД (воздуха высокого давления). Имел место полуанекдотический случай.
Обычно для прокатки трубы берется трубная заготовка, в ней делается осевая полость на прошивном стане и затем катается труба. С. М. Шулькин предложил иную технологию: на ВСМОЗ высверливать в слитке осевую полость, стружку возвращать в плавку, а слиток с полостью, минуя прошивной стан, сразу запускать в прокатку трубы. Получалась значительная экономия средств и времени.
Это предложение было опробовано, установлена его эффективность, и все дружно приняли решение снизить цены на титановые баллоны (конечно, в расчете на хорошую премию). Вопрос всем казался настолько очевидным, что меня, тогда еще очень молодого и неопытного, снабдили всеми материалами и послали в бюро цен Госплана получить справку о снижении цен на баллоны. Я приехал, доложил этот вопрос какому-то начальнику и получил ответ, меня ошеломивший: «Баррикадам» на оставшиеся два года пятилетки было запланировано 438 баллонов и если цену баллонов уменьшить на 20–25 процентов, то завод по этой позиции не выполнит план «по валу» на эти самые проценты. Поэтому менять цены на исходе пятилетки нельзя, а план – это закон. И мы ждали конца пятилетки, откорректировали цены и план на следующие годы и только после этого получили долгожданную премию. Вот такие казусы были в прошлой жесткой плановой системе.
А далее пошли другие задачи. Кингстоны и другие клапаны, крышки торпедных аппаратов, приводы торпедных аппаратов, тарельчатые и витые пружины, амортизаторы и множество других изделий, которые на флоте именуются дельными вещами. Работники института прошли через все это. У них не было понятия: «Это не мое, не моя специальность». Они влезали во все и брались за решение любого вопроса, необходимого для постройки корабля. И в этом я вижу высокий интеллект коллектива ЦНИИ КМ «Прометей».
На Севмаше
Пока специалисты ЦНИИ КМ «Прометей» решали свои задачи на рудном, металлургическом, сварочном и других производствах, корабль строился и рос день ото дня. Главный конструктор по корпусу Н. И. Антонов ввел за правило минимум раз в два-три месяца бывать в цехе и участвовать в работе бригады, курирующей ход строительства.
Обычно это было и серьезно, и смешно. В те времена надевать каску при входе в зону работ было необязательно, и Антонов ею не пользовался. А лысина у него была, как солнечный диск. В это время возникла проблема «тычков». На корпус лодки изнутри приваривалось множество скобок для размещения на них кабелей и труб. Их было тысячи. Швы считались малоответственными, но наши сварщики относились к ним серьезно, так как если в этом шве будет окисление, то в прочном корпусе возникнет трещина и это может плохо кончиться. Как потом выяснилось, он хорошо понимал это и старался осмотреть шов приварки каждого «тычка». И вот, переходя из отсека в отсек, он выпрямлялся, ударяясь головой о «тычок», приваренный к перегородке или пайоле на борту, так что на лысине появлялась очередная ранка. Вначале это вызывало смех и у него, и у нас, его сопровождавших. Но когда мы проходили два-три отсека и на голове его появлялись кровоточащие раны, это было уже не смешно, но тем не менее он готов был целыми днями лазать по отсекам, забираясь в самые потаенные уголки, перепроверяя работу контролеров и сварщиков. У него было высокое чувство ответственности как главного конструктора корпуса первой в мире цельнотитановой подводной лодки.
А на заводе все прекрасно понимали, что при постройке такого сложного инженерного сооружения, как корпус подлодки из совершенно нового материала – титана, требовался новый подход. Надо отдать должное – директор СМП Е. П. Егоров, его заместители, конструкторы, строители, цеховые работники приложили много усилий для создания небывалого производства.
Цех № 42 стал поистине полигоном новизны: ежедневное мытье полов, отсутствие сквозняков, освещенность, чистая одежда сварщиков и других рабочих, высокая культура производства стали его отличительным признаком. Большой вклад в становление цеха внес Р. И. Утюшев – замначальника цеха по сварке. Много умения и души вложили в это дело замечательные специалисты – северяне Ю. Д. Каинов, М. И. Горелик, П. М. Гром, военпред Ю. А. Беликов, А. Е. Лейпурт и многие другие – технологи, мастера, рабочие.
В результате было создано самое совершенное сварочное производство с аргоногелиевой защитой. Аргонодуговая, ручная, полуавтоматическая, автоматическая и другие способы сварки стали обычными для всех работников цеха. Здесь были отработаны сварка погруженной дугой, сварка в «щель» (без разделки), требования к качеству аргона (точка росы), появилась новая профессия – сварщик по защите обратной стороны шва (поддувальщик).
В этом цехе возникла такая эффективная форма сотрудничества производственных и научно-исследовательских коллективов, как постоянно действующая бригада. Возглавлял ее П. М. Гром, от ЦНИИ-48 постоянными членами были Б. В. Кудояров, И. С. Фатиев, З. Ф. Загудаева, от СМП Р. И. Утюшев, от ЦНИИ-136 Б. А. Эрам и другие классные специалисты. Все вопросы, возникавшие при постройке корпуса и его насыщении, эта бригада решала на месте. А вопросов было множество: например, как маркировать детали – клеймами или керном, можно ли их сваривать без сквозного проплавления (то есть допускать конструктивный концентратор), как приваривать «бобышки» (вертикальные стерженьки), как ремонтировать швы с вольфрамовыми включениями и окисленными участками, как защищать обратную сторону шва при сварке стабилизаторов.
Были тысячи вопросов, которые в основном решались на основе инженерной интуиции и производственного опыта. Это был принципиально новый подход к постройке таких сложных инженерных сооружений, как корпуса подлодок из нового материала, с использованием новых способов сварки. И он себя оправдал, так как позволил оперативно и четко принимать технические решения, не задерживая производство. И вот пришло время проводить гидравлические испытания. Первым тестировали средний блок. Вечером цех № 42 был освобожден от всех работников, остались только члены государственной комиссии и бригада специалистов, обеспечивавшая нагружение. Вот ступенями повышается давление: 10–20–30–40 атмосфер, выдержка... и вдруг за пять минут до конца выдержки происходит разрушение. У всех состояние шока.
На следующий день воду слили и обнаружили, что трещина длиной почти два метра возникла в обшивке – на границе между двумя комингсами килевых кингстонов, расположенных очень близко друг к другу и к плоской переборке. Этот узел был очень жестким и, естественно, стал местом концентрации напряжений, когда упругоподатливая обшивка стала расширяться при внутреннем нагружении. Здесь и произошло разрушение. Впоследствии подобные трещины возникали и в других «жесткостях» – в районе окончания поперечного шельфа как основы для турбины, в окончании книц.
На этом опыте возникла новая концепция проектирования оболочковых конструкций: исключаются «жесткие» окончания, появляются «мягкие» кницы, плавные переходы от жестких деталей к упругоподатливым и т. д. Эта идея в полной мере была реализована затем В. Г. Тихомировым и В. В. Крыловым при проектировании ПК подводной лодки проекта 705 «Лира» (по кодификации НАТО – «Альфа»). С учетом опыта Н. И. Антонова их корпус оказался идеальным. Но после всех неприятностей корпус подлодки проекта 661 был доведен до совершенства и все блоки прошли испытания.
Проект «Анчар» был необычен не только корпусом из титанового сплава. На лодке впервые были применены ПКР «Аметист» с подводным стартом и забортным расположением шахт, созданы гидроакустическая станция и гидроакустический комплекс, которые в сочетании с торпедными аппаратами предопределили совершенно новую форму носовой оконечности – шаровую вместо привычно остроносой. Это логично привело к каплевидной форме корпуса до кормы. Двойная энергоустановка с двумя турбозубчатыми агрегатами и двумя линиями гребных валов привела к новой форме кормовой оконечности (так называемые штаны), когда два длинных конуса заканчивались гребными винтами. Изящное ограждение рубки, кормовой стабилизатор придавали кораблю элегантно-красивый вид. В нем было хорошо и внутри: cияющие чистотой кают-компания, комната отдыха, душевая, сауна, титановые унитазы. Антонов очень гордился тем, что на подлодке созданы условия для экипажа не хуже, чем на надводном корабле. Это потом подтвердил командир лодки, который служил на ней с момента постройки, ходил и в Арктику, и в Антарктиду, и в Карибское море, и в Тихий океан.